蜗轮蜗杆传动
大约 7 分钟
蜗轮蜗杆传动
仅讨论普通圆柱阿基米德蜗杆传动
传动特点
基本参数
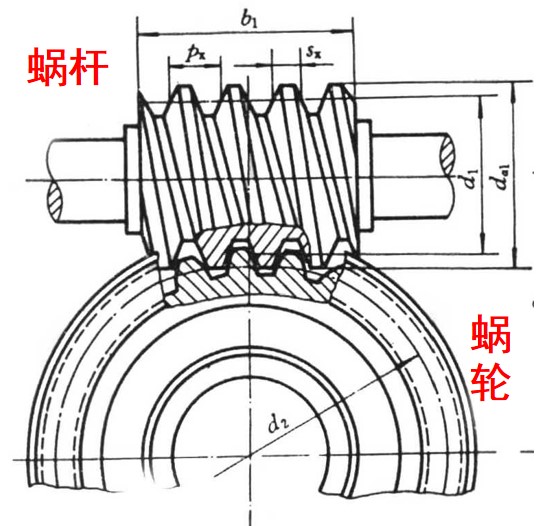
- 定义蜗轮蜗杆传动的几何尺寸以中间平面上的尺寸为主, 中间平面即过蜗杆轴线, 垂直于涡轮轴线的平面
- 在中间平面下, 蜗轮蜗杆相当于齿轮齿条啮合
- 通常蜗杆为主动件, 蜗轮为从动件, 因此蜗杆的参数采用下标
蜗杆的基本参数
为了简化蜗杆制造, 蜗杆的外形已完全标准化, 并通过铣削加工蜗杆, 滚刀加工蜗轮, 因此, 以下参数均为标准值
名称 | 符号 | 含义 |
---|---|---|
蜗杆头数 | 即蜗杆上螺旋线的数目 | |
蜗杆分度圆直径 | 蜗杆分度圆上采用标准值, 其中蜗杆分度圆直径也属于标准值 | |
模数 | 由蜗杆特性可得, 蜗杆轴向与蜗轮端面上模数相同 | |
压力角 | 对于普通圆柱阿基米德蜗杆传动, 采用标准值 , 并且蜗杆轴向与蜗轮端面上压力角相同 | |
直径系数 | 由于蜗杆的模数与分度圆直径均为标准值, 因此定义其比值为直径系数 , 注意与齿轮不同, 得到的结果不是齿数 |
蜗杆几何尺寸
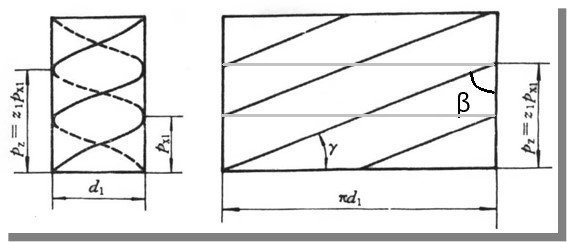
分度圆柱面上的尺寸
- 螺旋线在分度圆柱面上的投影如图左侧图形
- 同一螺旋线在蜗杆轴线方向的距离为导程
- 相邻螺旋线在蜗杆轴线方向的距离为螺距
- 由于中间面上, 蜗杆的投影为齿条, 齿条齿距即相邻螺旋线在蜗杆轴线方向的距离, 因此螺距满足 (蜗杆在轴向与端面上模数相同)
圆柱面展开尺寸
- 在蜗杆的分度圆柱面上展开可得到如图矩形
- 螺旋线在展开矩形上呈平行斜线, 其中同一条螺旋线的投影在矩形的左右交点连线平行于端面
- 定义螺旋线与端面的夹角为导程角 , 由图可得, 导程角满足
- 定义端面与法面的夹角为螺旋角, 螺旋角与导程角满足关系
蜗轮蜗杆传动参数
啮合条件
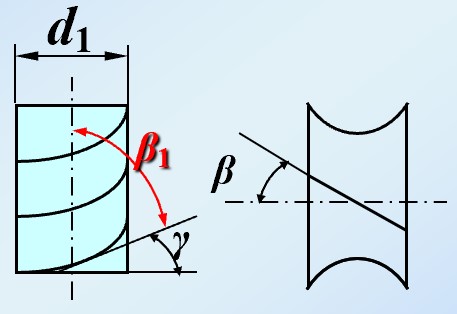
当蜗轮蜗杆的轴线交错角为 时, 蜗轮蜗杆正确啮合需要满足蜗轮的螺旋角与蜗杆的导程角大小相同, 且旋向相同, 即
传动比
- 对于蜗杆的分度圆柱展开, 螺旋线与矩形一侧的交点相当于蜗杆中中间面上齿条的齿形
- 蜗杆转动一圈, 相当于矩形边从一侧移动到另一侧 (方向由转向决定), 矩形边与展开螺旋线的交点反映了齿条齿形的移动
- 因此可得, 蜗杆转动一圈, 等价于中间面上的等价齿条移动一个导程
- 蜗轮在中间面的投影为齿轮, 因此蜗杆转动一圈, 等价齿轮转动
- 可得蜗轮蜗杆传动满足关系 (注意与齿轮不同, 蜗杆传动的出动比不能使用分度圆的比值)
变位系数
- 通常仅对蜗轮进行变位, 即仅有变位系数
- 与齿轮齿条相同, 变位后中心距满足
其中 为变位后的中心距
- 由齿轮齿条变位得, 变位时分度圆上齿宽与齿距变化, 但仍为节圆 (齿条齿形压力角处处相等, 为标准压力角, 因此节点依然为分度圆)
- 蜗轮蜗杆变位通常用于凑中心距与微调传动比
设计分析
相对滑动
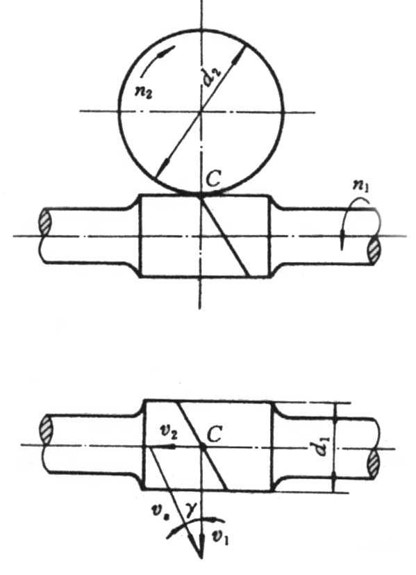
- 对于齿轮传动, 两齿轮为纯滚动, 接触点上不存在滑动, 因此传动效率高
- 对于蜗轮蜗杆传动, 令蜗轮静止, 蜗杆相对于蜗轮运动, 在接触点处存在相对滑动
- 相对滑动速度的两个分速度分别来自蜗杆转动 与蜗轮转动
- 由于
可得两个速度之间的夹角为
- 因此滑动速度大小满足
受力分析
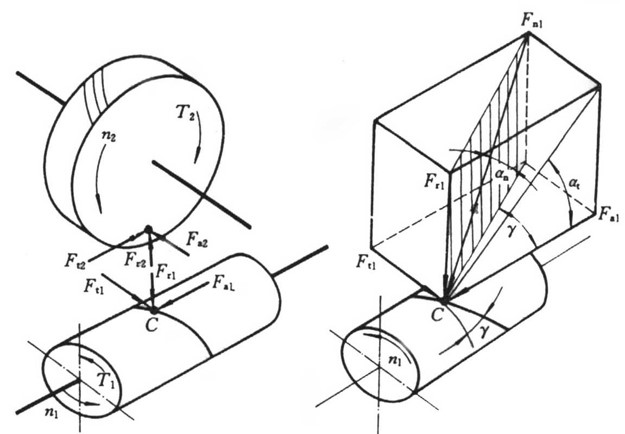
- 通常蜗杆为主动轮, 因此蜗杆以 为下标
- 接触点上的力垂直齿面指向蜗轮 / 蜗杆内部
- 由于齿形为螺旋形, 因此接触力共可分解为三个方向的力
- 注意由于蜗轮蜗杆轴线垂直, 因此两零件的径向与圆周方向不同
蜗杆受力
- 蜗杆作为主动轮, 受到一个阻碍其转动的圆周力 , 与其转动方向相反, 并在接触点上与分度圆柱面像切
- 由于齿面倾斜 (相对于水平面) , 接触点上的径向力 垂直齿面向里
- 由于螺旋状的齿形, 因此蜗杆还收到一个轴向力 , 可通过右旋右手定则, 根据蜗杆转向确定
蜗轮受力
- 蜗轮作为从动轮, 圆周力 为动力, 与蜗轮转向相同, 与蜗杆的轴向力 平衡
- 同样蜗轮也有径向力 并于蜗杆的径向力平衡
- 蜗轮的轴向力 与蜗轮的圆周力 平衡
转矩关系
- 通过传递的功率表示转矩有
- 因此蜗杆与蜗轮转矩满足关系 (注意由于蜗轮传动效率低, 需要考虑机械效率 )
- 因此蜗轮的转矩满足 (蜗杆转矩通过传递效率计算)
机械效率
- 蜗杆传动总效率包括
- 啮合损耗功率
- 轴承摩擦损耗功率
- 搅油损耗功率
- 总效率满足
- 定义当量摩擦角 , 与摩擦系数满足关系
- 当蜗杆主动时, 近似满足
- 随 增大而增大, 而 随头数增加而增加
- 因此增加头数可以增大传动效率, 但一般 , 继续增大将导致加工难度增大, 且效率提升低
- 认为 或 时, 蜗轮蜗杆具有自锁性, 此时一般有
失效形式
蜗杆采用耐磨强度高的 45钢或合金钢, 蜗轮则采用磨擦系数低的铜合金 (高速使用铸锡青铜, 低速使用铸铝青铜), 由于铜合金强度低, 因此一般失效发生在蜗轮上
齿面点蚀与胶合
- 当蜗轮材料为铸锡青铜时, 主要失效形式为齿面点蚀
- 当蜗轮材料为铸铝青铜时, 主要失效形式为齿面胶合
- 对于两种失效形式, 均需要校核齿面的接触疲劳强度
- 由于高温下容易导致齿面胶合, 且蜗轮蜗杆传动摩擦发热大, 因此还需要热平衡计算
齿面折断
仅当 或强烈冲击载荷时可能发生, 需要校核弯曲强度, 一般不校核
接触疲劳强度计算
- 由于中间平面上蜗杆传动类似于斜齿条斜齿轮传动, 使用赫兹公式计算接触强度, 公式按斜齿轮推导
- 设计时, 通过疲劳强度计算得到 , 并通过此参数选择蜗杆参数 ( 与 均为标准值)
润滑与散热设计
润滑
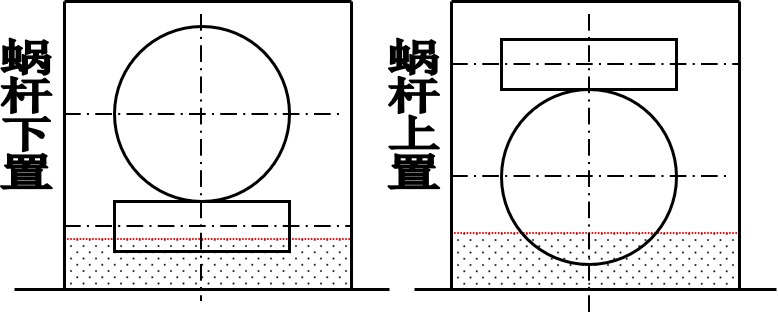
- 当 , 采用蜗杆下置, 搅油损耗大, 但润滑效果好
- 当 , 采用蜗杆下置, 避免搅油损耗
散热
由热平衡条件可得, 增大散热面积与改善散热条件可以降低热平衡时的工作油温, 因此可采用以下方法降低油温
- 在箱体外壁增加散热片
- 在蜗杆轴端增加风扇
- 在油池中使设置冷却管